Project description
Real estate developer’s expression of office architecture reflects Scandinavian concepts, thoughtful rationality, and restrained yet remarkably functional solutions.
Implementing the BIM process
One of the reasons we were determined to use BIM for this project was the complexity of the engineering components. The building consists of a number of laboratories requiring special temperature and environmental control. Another reason was the opportunity for the manufacturer of precast reinforced concrete elements to work together on the model, which saved additional time normally spent relaying the tasks of reinforcement and element production.
A BIM project coordinator was assigned in the initial stage of the project, along with a dedicated server for the model. The project parties were issued with several rules concerning model update intervals and splitting models into smaller parts.
Subsequent communication between designers and construction site specialists was handled through free-to-use Tekla BIMsight program. This made communication and coordination efforts easier throughout the entire design and construction process.
A BIM model was used at the construction site to gain visual (3D) information, coordinate between project sections, aid in reinforcing the monolithic concrete elements, install engineering systems, and control the quantities (using IFC models).
The Solibri program was used to check the quantities in subcontractors’ certificates of completed work. At that point it became clear that not all programs export a sufficiently informative IFC file, which prevented us from automatically checking the quantities of some of the engineering systems. A BIM model was used in the meetings at the construction site, and 3D images were printed as a visual aid for the assemblers.
Client
Vilniaus universitetas
Project area
24 084 m²
Construction cost
32,2 mln.
Software
AutoCAD, Tekla Structures, DDS-CAD
Benefits of our approach
- For the customer: better and more efficient communication between project parties; the ability to see project progress and have a clear understanding of the end product.
- For the designers: easier work and better communication between project parties; fewer mistakes; exact quantities.
- For the builders and manufacturers: collaboration between designers and manufacturer during the modelling stage; visual and more comprehensible information from the model; fewer mistakes at the construction site.
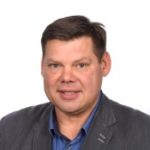
“It’s the first project in Lithuania where all of the segments were designed in the BIM environment and used during the construction process. The manufacturers of structural parts worked on the same model simultaneously, which assisted in the confirmation of all the linkages and parts, and accelerated the production and delivery process.”